Intelligent automation for intralogistics processes
Solutions along the material flow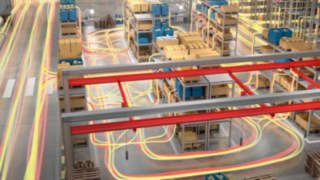
Modern intralogistics is facing growing challenges: online retail and personalized mass production are generating ever-increasing volumes and leading to ever more fragmented processes. Perfectly structured processes are essential in order to meet these demands. A key element for creating an efficient, continuous material flow is a comprehensive understanding of all intralogistics processes, from the receipt of goods through to storage and production supply, as well as dispatch.
Thanks to our extensive hardware expertise, Linde Material Handling has a profound understanding of all relevant material flow processes. This detailed process knowledge enables integrated optimizations, whose effectiveness is not dependent on the specific truck solution. A key factor of efficient process design is intelligent automation, from the individual process step through to the complete material flow. We establish this foundation through expert advice, which precisely analyzes the current situation on site and develops an individually tailored solution from existing system components.
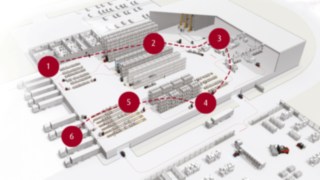
Six steps to efficiency
Modern intralogistics relies on well-structured and accurately planned material flows. A company’s intralogistics material flow usually involves six separate process steps, whose specific requirements offer a range of potential optimizations.
1. Goods in
Every internal material flow starts with unloading goods in the goods in area. An incorrectly planned or poorly organized goods in area can lead to considerable disruptions in the process flow. The goods in area is where the goods are unloaded, checked, sorted, labeled, and prepared for onward transport to an interim storage area or production. Short process times, low space requirement, minimum involvement of employees, and high process quality are essential criteria for the success of this step.
2. Storage
The warehouse is at the heart of all internal processes. Ideally, it makes optimum use of the available storage area and enables the efficient storage of different types and sizes of goods. The load units need to be transported to the intended storage and transfer areas quickly and reliably. Short throughput times, transparent processes, and a high level of flexibility during storage are all features of well-organized warehousing.
3. Production supply
Bringing material and goods to the right place at the right time is the central goal of efficient production supply. Whether automated or manual, materials can be supplied to the production area, especially assembly lines, using a range of different concepts that use different technology, storage stages, or process organization. Ideally, this creates an intelligent, controlled, and continuous movement of goods with minimum expenditure of energy and costs.
4. Order picking
Efficient order picking processes have the potential to noticeably improve a company’s competitiveness. Materials and goods need to be quickly and efficiently combined from a specific overall range and prepared for timely delivery. The picking order is transmitted to the order picker in the form of analog or digital pick lists. In this case, the order picker may be a person or an automated truck. To fully exploit the economic potential of the order picking phase, picking processes must be fast, precise, and transparent.
5. Dispatch
Dispatch is closely linked to order picking. Products and goods need to be consolidated and bundled into units ready for dispatch to enable the greatest possible standardization of storage and transport. A range of automation options are available for designing these processes more efficiently and so reducing transport and dispatch costs. The right warehouse management systems make all flows of goods and materials more transparent and optimize control.
6. Goods out
The goods out area is where goods are provided from the warehouse. After a final identity and quality check, individual packages are combined and positioned on the staging area ready for shipment. In some cases, external goods with unknown content also need to be integrated into the shipments. Even the smallest errors in the goods out area can bring the entire process chain to a standstill. A fast, well-organized, and transparent flow of goods is critical in this phase.
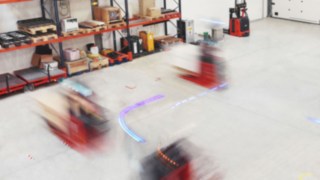
The next level: automation
Automation can be an important element in comprehensively optimizing internal material flows. The use of automated industrial trucks is particularly beneficial wherever transport and storage tasks need to be permanently repeated.
Advantages at a glance
Applications for automation solutions
Automated trucks can be integrated into the material flow in countless ways. Depending on the specific requirements, they take over different transport tasks and ensure a constant and continuous flow of goods. Whether floor to floor transport, floor to rack, or conveyor technology to conveyor technology: automated solutions make sense wherever standardized applications are involved.
Floor to floor
In automated floor to floor applications, the truck picks up the load unit from the floor and places it back down on the floor at the destination. The load carriers are placed in defined zones for pick up and transported to specified destinations. The benefit of floor to floor applications is that, apart from an automated truck, no further automated devices are required. This means that they can be integrated into almost all phases of the intralogistics process. They can transport load carriers from the goods inward area to the warehouse, from the warehouse to production, or from production to goods outward. Floor to floor applications are a good choice wherever large numbers of components need to be available in a confined area at the right time.
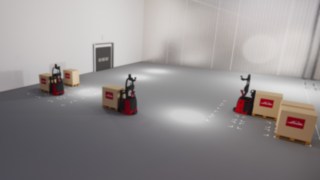
Floor to floor - reference example
Fritz Holter GmbH, an Austrian plumbing and heating wholesaler relies on this ‘magic pair’ in its plant, or Franzl and Gustl, as they have been affectionately christened by employees. The two automated guided vehicles (AGV) from the L-MATIC series of the provider of material flow solutions, Linde Material Handling, work in two shifts and support the order picking team on site. Whenever they are required, the order picker simply pushes a button to summon them for a transport along the defined red or green route. Franzl or Gustl then independently makes its way to the fixed storage area using the requested red or green route – day in, day out, without needing any complex software. In addition, there was no need to change the infrastructure; pedestrians and trucks still move along the same routes – accident-free, naturally. The tireless dedication of Franzl and Gustl lets employees focus more on the order picking, so they make fewer errors and work more efficiently. And goods arrive at the requested destination almost like magic.
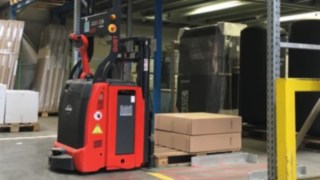
Floor to conveyor technology
Floor to conveyor technology applications can be used in all phases of the intralogistics process. In the goods inward area, automated trucks pick the load units off the floor and transport them to the relevant storage areas. There, they transfer the goods to the conveyor technology used in the warehouse. This may be a fully-automated parts warehouse or a high rack warehouse with automated very narrow aisle trucks. Another common application is the use of automated trucks to pick up the finished goods from the conveyor belt after production. From there, they transport the load unit for automatic palletizing and wrapping, either to the warehouse or directly to the goods outward area, where the load unit is placed on the floor.
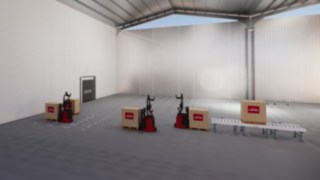
Floor to conveyor technology - reference example
In large warehouses, loaded pallets often have to cover long routes in order to, for example, reach the conveyor belt from their storage location. If this is performed manually, this is usually associated with considerable time and expense. The solution, naturally, is: automation. At a large manufacturer of paper-based packaging in southern Germany, for example, automated guided vehicles (AGV) reliably and safely transport the goods from their arrival point to the required conveyor system at the right time. The AGV recognizes and positions the goods on the conveyor system completely independently. This requires simple light barriers that are installed on the conveyor technology. They allow the AGV to automatically position the pallet or even to retrieve it and then transport it along a fixed route across the warehouse to its destination.
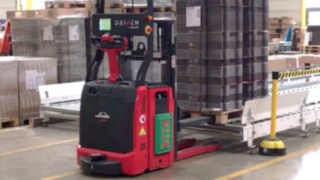
Conveyor technology to conveyor technology
Conveyor technology to conveyor technology applications are primarily used to transport load units between stationary automatic systems. For example, automated trucks deliver required parts from the exit of the automated warehouse to the automated supply point of a production machine. After the production process, the goods are either transferred back to the automated warehouse or transported to the next processing step (e.g. to the foil wrapping machine). The goods are then taken to the dispatch area. Here, automated trucks often transfer the load units to gravity tracks to assign them directly to a delivery gate or a specific delivery truck.
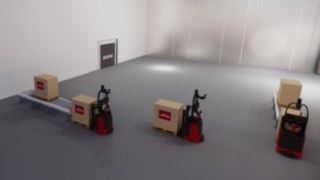
Conveyor technology to conveyor technology - reference example
Higher demand and double the production numbers with unchanged infrastructure – this is precisely where automation can make a big difference, as is the case at Massilly France. The French manufacturer of packaging materials was looking for a solution to automatically stack its goods and prepare them for transport. And it found just what it was looking for: a Linde L-MATIC transports the pallets from the automatic palletizing robot to the automatic foil wrapping machine, waits until the cardboard boxes are wrapped, and then transports them on to the warehouse. “The exciting thing about the Linde L-MATIC solution for us is that it is constantly developing and does not require us to change our infrastructure,” says Patrice Ferrero, Production Manager at Massilly France. The ease of use and flexible loading options allow the AGVs to be smoothly integrated into the existing processes and enable Massilly France to keep production running at full speed. Meanwhile, 4 AGVs are now in use with additional integrations in planning.
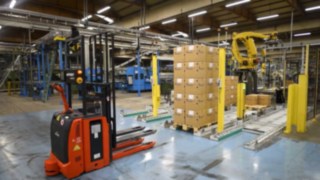
Conveyor technology to rack
Conveyor technology to rack applications are popular where the interim storage of the load unit is necessary to ensure a continuous supply to the production machinery. Automated trucks transport the required parts from the rack in the interim storage area to the production machinery’s upstream conveyor belts. This is followed by the transport from the machine back to the rack where the parts are then once again temporarily stored before they leave the warehouse. Conveyor technology to rack applications are often used by automotive suppliers to adapt precisely to the synchronized production requirements of car manufacturers. In the packaging industry, the conveyor technology transports the finished goods to machines in the dispatch area where they are provided for delivery on gravity tracks or racks.
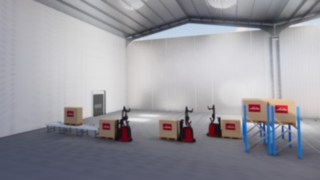
Floor to rack
Floor to rack applications are available for a huge range of different areas. They are often used in goods inward areas to store the incoming goods in racks. From the warehouse, the goods can then be transported to floor spaces where they are collected by employees. Floor to rack applications are extremely flexible and versatile, as no special installations are required to place the load units on the floor. Alternatively, the goods can be transported from the floor to an additional rack for interim storage. This option is often used to ensure a timely supply for production machines, even if the main warehouse is far away from the processing location.
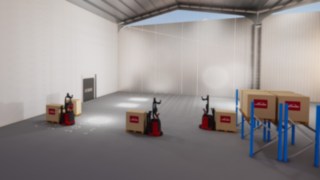